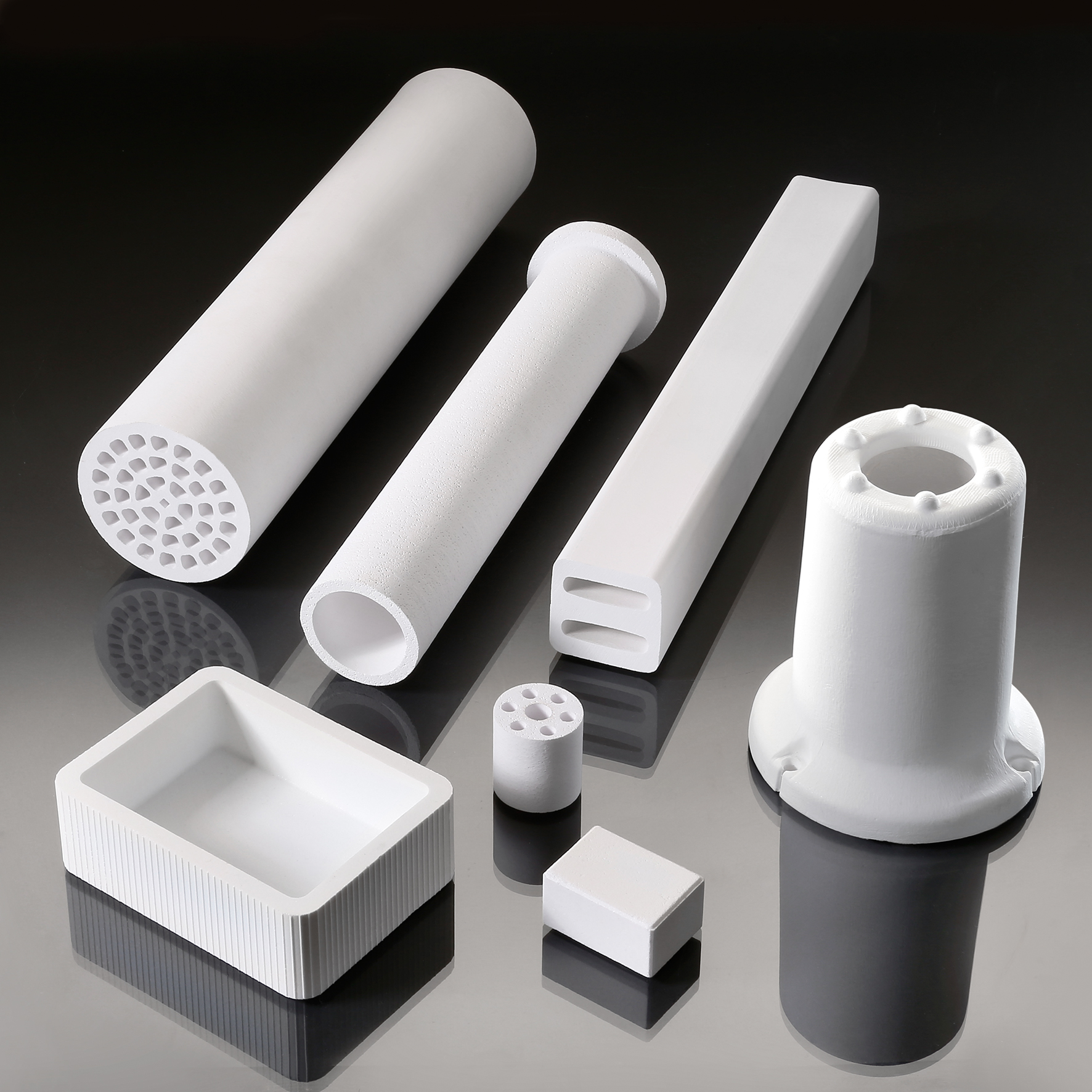
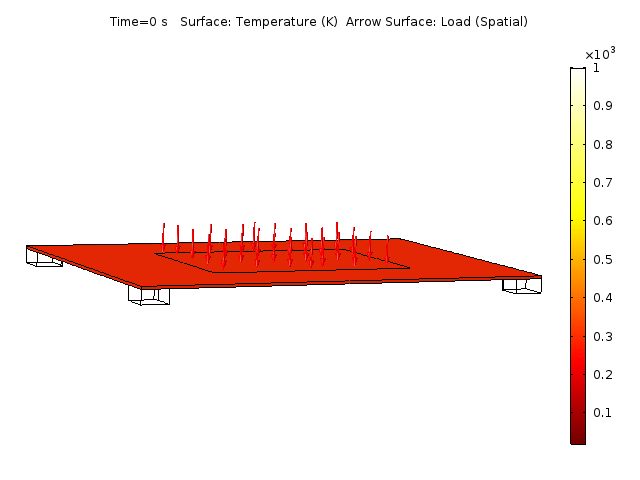

Brennhilfsmittel werden in Wärmeprozessen bei der Produktion von stückigem Erwärmungsgut wie Keramik- oder Metallbauteilen eingesetzt. Die Brennhilfsmittel tragen dabei das Erwärmungsgut und sollen gewährleisten, dass sich die Bauteile weder verformen noch miteinander verkleben. Um eine hohe Produktqualität und eine geringe Ausschussrate zu erzielen, soll das Erwärmungsgut unabhängig von der Position im Ofen möglichst homogen und einheitlich erwärmt und abgekühlt werden. Beim Wärmemanagement im Ofen kommt den Brennhilfsmitteln eine wichtige Rolle zu. Auch die Wechselwirkung des Erwärmungsguts mit der Ofenatmosphäre wird durch die Brennhilfsmittel stark beeinflusst. Zur Kontrolle des Gasaustausches werden neben unterschiedlichen Trägern und Platten häufig auch Kapseln benötigt, in denen das Erwärmungsgut platziert wird.
Zusätzlich zum Erwärmungsgut müssen bei Wärmebehandlungsprozessen immer auch die Brennhilfsmittel erhitzt werden. Dadurch steigt der Energieverbrauch, bei Prozessen mit kleinen Bauteilen oft um das Doppelte. Brennhilfsmittel sind Verschleißteile, die durch die thermomechanischen und chemischen Belastungen beim Einsatz regelmäßig ausgetauscht werden müssen. Ihre Herstellung verursacht zusätzlichen Energieaufwand und erhöht die Betriebskosten der Ofenanlagen. Um die Energieeffizienz der Wärmeprozesse zu steigern und die Kosten zu reduzieren, müssen die Wärmekapazität der Brennhilfsmittel verringert und deren Lebensdauer erhöht werden.
Um die Wärmekapazität von Brennhilfsmitteln zu verringern, werden am Fraunhofer-Zentrum HTL Werkstoffe für Brennhilfsmittel gezielt optimiert. Die Verringerung der Masse der Brennhilfsmittel wird durch eine dünnwandigere Auslegung und/oder einer Steigerung der Porosität der Brennhilfsmittel erzielt. Beide Ansätze haben jedoch einen negativen Einfluss auf die Tragfähigkeit. Während es bei tiefen Temperaturen durch die erhöhten Spannungen leichter zum Versagen durch Bruch kommt, tritt bei höheren Temperaturen eine verstärkte Verformung durch Kriechen ein. Brennhilfsmittel mit hoher Tragfähigkeit bei gleichzeitig geringer Masse stellen eine besondere Herausforderung bei der Werkstoffentwicklung dar.
Zur bestmöglichen Orientierung in diesem Zielkonflikt stehen am Fraunhofer-Zentrum HTL Finite-Elemente (FE)-Methoden zum Materialdesignund Bauteildesign zur Verfügung. In einfachen Fällen, wie in dem genannten Beispiel, können jedoch auch so genannte Materialindizes sehr hilfreich sein. Alle für den konkreten Anwendungsfall relevanten Materialeigenschaften und Randbedingungen werden zu einer einzigen Kennzahl, dem Materialindex, kombiniert, der dann zu optimieren ist[1]. Um ein plattenförmiges Brennhilfsmittel mit geringer Kriechverformung bei gleichzeitig möglichst geringer Wärmekapazität auslegen zu können, werden beispielweise die Dichte, die spezifische Wärmekapazität und die uniaxiale Viskosität des Werkstoffs zu einem Materialindex kombiniert. Mit diesem Ansatz können Benchmark-Tests anhand einer einzigen Kennzahl durchgeführt werden. Am Fraunhofer-Zentrum HTL konnten poröse Brennhilfsmittel mit deutlich gesteigerter Performance im Vergleich zu kommerziellen Produkten entwickelt werden.
Am Anfang der Entwicklung von Brennhilfsmitteln steht die Versatzentwicklung. Dabei werden die keramischen Rohstoffe sorgfältig aufbereitet und mit verschiedenen Additiven möglichst homogen vermischt. Die keramischen Massen werden anschließend über verschiedene Formgebungsverfahren, wie z. B. Schlickerguss oder Feuchtpressen, weiterverarbeitet. Dabei ist wichtig, die Scherben schonend und ohne Defekteintrag zu trocknen. Die Qualität der resultierenden Grünkörper ist die Basis für ein hochwertiges Endprodukt. Um die Qualität der Grünkörper bewerten zu können, werden am HTL spezielle Analyseverfahren eingesetzt. Nach der Formgebung und Trocknung folgt die Entbinderung mit anschließender Sinterung der Brennhilfsmittel. Der Sinterprozess wird mit den am HTL entwickelten Verfahren so eingestellt, dass die oben genannten Materialeigenschaften optimal aufeinander abgestimmt werden. Für die Ermittlung der Werkstoffeigenschaften stehen am Fraunhofer-Zentrum HTL unterschiedliche Analysemethoden zur Verfügung. Für eine gezielte Optimierung der Brennhilfsmittel ist es besonders wichtig, die Eigenschaften der Werkstoffe unter Anwendungsbedingungen zu kennen. Dafür wurden am Fraunhofer-Zentrum HTL ThermoOptische Methoden (TOM) zur Charakterisierung der Hochtemperaureigenschaften entwickelt. Für die Bewertung von Brennhilfsmitteln werden unter anderem das Thermoschock- und Thermozyklierverhalten, die Wärmeleitfähigkeit, die mechanischen Eigenschaften und die Kriechverformung bis zu sehr hohen Temperaturen ermittelt.
Am Fraunhofer-Zentrum HTL werden Brennhilfsmittel aus unterschiedlichen Keramiken entwickelt, als Prototypen hergestellt und ihr Einsatzverhalten wird getestet. Diese können oxidische Zusammensetzungen, wie z.B. Aluminiumoxid, Mullit, Cordierit oder Zirkonoxid, oder nichtoxidische Zusammensetzungen, wie z.B. SiC oder SiSiC haben. Neben Poren können auch keramische Fasern zur Verbesserung der Anwendungseigenschaften in die Brennhilfsmittel eingebracht werden. Für die Entwicklung von Prototypen mit komplizierter Geometrie werden 3D-Druckverfahren eingesetzt. Für korrosionsanfällige Brennhilfsmittel werden am Fraunhofer-Zentrum HTL keramische Schutzbeschichtungen entwickelt. Diese werden über nasschemische Beschichtungstechniken wie Tauchen, Sprühen oder Streichen appliziert und anschließend eingebrannt.
[1] Raether, F.: Ceramics Facing Competition with other Materials, Ceramic Applications, 4/2016, S. 57-61