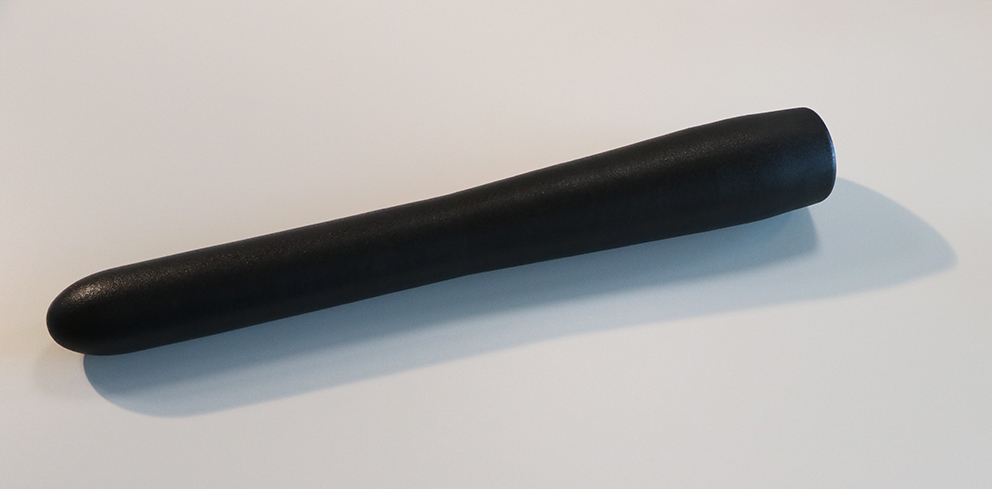
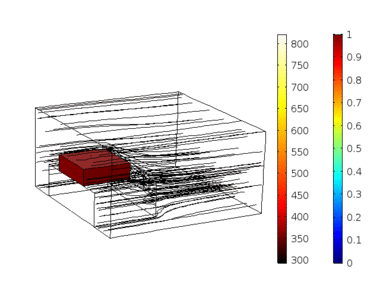
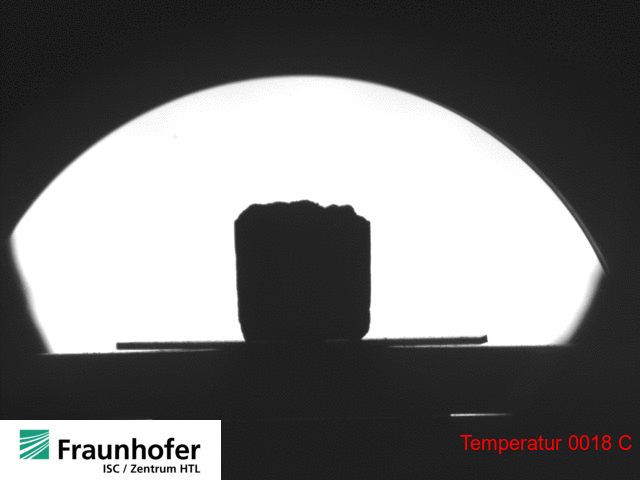
Bei der Herstellung von geformten Feuerfestwerkstoffen über die Pulverroute ist die Wärmebehandlung ein wichtiger Herstellschritt, der die Produktqualität prägt, der jedoch auch erheblich zu den Herstellkosten beiträgt. Entsprechend sorgfältig müssen die Prozessparameter bei der Wärmebehandlung optimiert werden. Bei der Trocknung und Entbinderung müssen Verfahren identifiziert werden, die einerseits einen möglichst hohen Durchsatz ermöglichen, aber andererseits die Schadensfreiheit der Bauteile gewährleisten. Gleiches gilt bei höheren Temperaturen für die Quarzumwandlung, die Carbonatzersetzung und die Entwässerung von Tonmineralen – falls die entsprechenden Bestandteile im Grünkörper vorhanden sind. Bei der Sinterung wird eine endformnahe Herstellung mit engen Fertigungstoleranzen und guten Materialeigenschaften angestrebt. Dabei sollen der Durchsatz durch den Brennofen maximiert und dessen Energie- und Wartungskosten minimiert werden. Eine besondere Herausforderung ergibt sich durch die bei Feuerfestwerkstoffen üblichen Produktgrößen, die ohne Optimierung oft zu besonders langen Temperaturzyklen führen.
Die Optimierung der Wärmebehandlung kann am HTL für alle Arten von Feuerfestmaterialien durchgeführt werden, z.B. für tonerdereiche -, Silica- oder basische Erzeugnisse, Schamotte oder Sondererzeugnisse, wenn diese über die Pulverroute hergestellt werden. Die am HTL eingesetzten Methoden eignen sich besonders für das Hochskalieren auf große Bauteile mit charakteristischen Längen im Dezimeter- bis Meterbereich. Für die Erfassung der notwendigen In-situ-Messdaten stehen ThermoOptische Messanlagen (TOM) mit allen gängigen Atmosphären zur Verfügung: Luft, Inertgas sowie Brenngasatmosphären wie sie in gasbeheizten Öfen vorliegen. Je nach Atmosphäre können Maximaltemperaturen zwischen 1700°C und 2200°C dargestellt werden. Alle für die Optimierung der Wärmebehandlung von Feuerfestwerkstoffen erforderlichen Materialeigenschaften können in situ gemessen werden. Die In-situ-Messungen werden an Proben mit einem Volumen von ca. 30 cm³ bis 100 cm³ durchgeführt. Die Hochskalierung auf den Bauteilmaßstab erfolgt mit Finite-Elemente (FE)-Verfahren. Für alle wesentlichen Wärmebehandlungsschritte an Feuerfestwerkstoffen stehen entsprechende FE-Modelle zur Verfügung. Mittels FE-Simulation werden die Prozessparameter optimiert und anschließend im Ofen bei definierten Bedingungen experimentell verifiziert. Im letzten Schritt werden die optimierten Prozessparameter dann auf den Produktionsofen übertragen.
Bei der Trocknung muss das in den Grünteilen noch enthaltene Wasser entfernt werden, ohne dass es zu Schäden an den Bauteilen kommt. Bei Feuerfestwerkstoffen können aufgrund der Bauteilgrößen erhebliche Trocknungsspannungen auftreten. Eine zu schnelle oder ungleichmäßige Trocknung führt zu Rissen oder Verzug. Dabei sind die lokalen Trocknungsraten stark von der relativen Feuchte, der Temperatur und der Strömungsgeschwindigkeit des Trocknungsgases abhängig. Das HTL verfügt über eine Vorrichtung, mit der Proben unter kontrollierter Feuchte, Temperatur und Gasströmung während der Trocknung gewogen werden können. Auf diese Weise kann die Trocknungsrate während der verschiedenen Trocknungsstadien ermittelt werden. In den kritischen Stadien kann die Trocknungsrate gezielt abgesenkt werden. Der Verzug der Bauteile durch ungleichmäßige Trocknung wird in FE-Modellen simuliert, bei denen die Gasströmung und der lokale Feuchtegradient berücksichtigt werden. Bei der Optimierung werden Feuchte- und Strömungsmessungen in den industriellen Trocknungsaggregaten berücksichtigt.
Bei der Entbinderung werden die in den Grünteilen enthaltenen organischen Formgebungsadditive wie Binder, Plastifizierer oder Dispergiermittel thermisch entfernt. Die organischen Additive werden dabei in sauerstoffhaltiger Atmosphäre ausgebrannt oder in reduzierender bzw. inerter Atmosphäre pyrolysiert. Beim Binderausbrand wird lokal Wärme freigesetzt – während bei der Pyrolyse Wärme verbraucht wird. Die entstehenden Temperaturunterschiede bewirken thermische Spannungen, die wiederum zu Rissen oder zur Zerstörung der Grünteile führen können. Bei zu schneller Entbinderung können die entstehenden Gase nicht rasch genug aus den Porenkanälen an die Bauteiloberfläche transportiert werden. Der entstehende Überdruck in den Porenkanälen führt ebenfalls zu Bauteilschäden. Daneben gibt es noch weitere unerwünschte Phänomene, die bei der Entbinderung auftreten können, z. B. die Entzündung von Schwelgasen im Ofenraum. Ähnlich wie bei der Trocknung gilt es, das schnellste noch sichere Temperaturprofil zu finden, mit dem die Entbinderung fehlerfrei durchgeführt werden kann. Strömungsgeschwindigkeit und Zusammensetzung der Ofengase können dabei in vielen Fällen variiert werden.
Analog zur Trocknung werden Entbinderungsexperimente am HTL bei kontrollierter Atmosphäre und Temperatur durchgeführt. Der Entbinderungsgrad wird durch die Messung der Probenmasse verfolgt, Rissbildungen werden durch Schallemissionsanalyse detektiert. Die Optimierung der Entbinderungsparameter erfolgt analog zur Trocknung mittels FE-Simulation, die Verifizierung der optimierten Bedingungen durch zusätzliche Entbinderungsexperimente. Ähnlich wird auch bei anderen thermischen Reaktionen vorgegangen, die Gase freisetzen, z. B. bei Entwässerung oder Carbonatzersetzung.