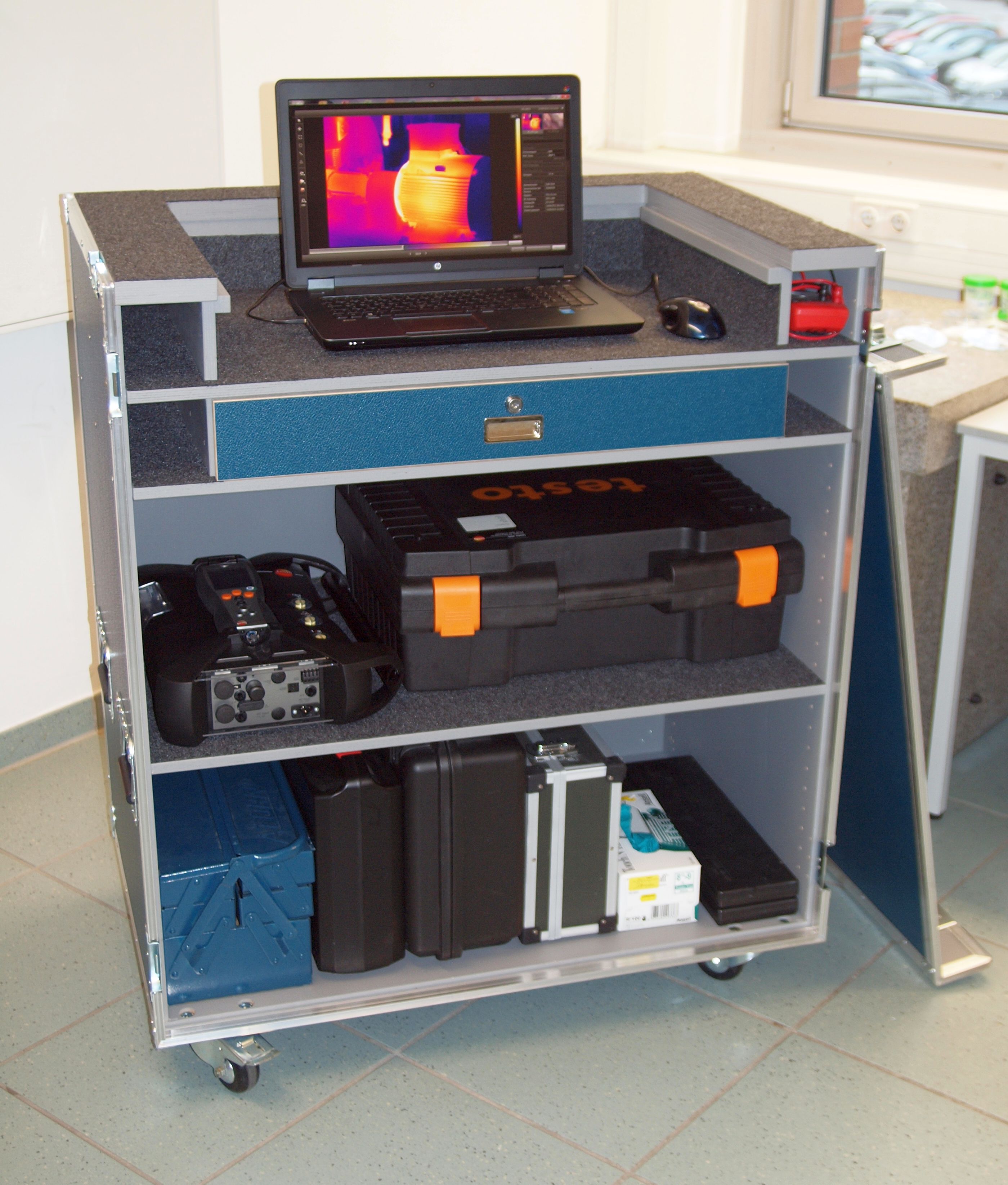
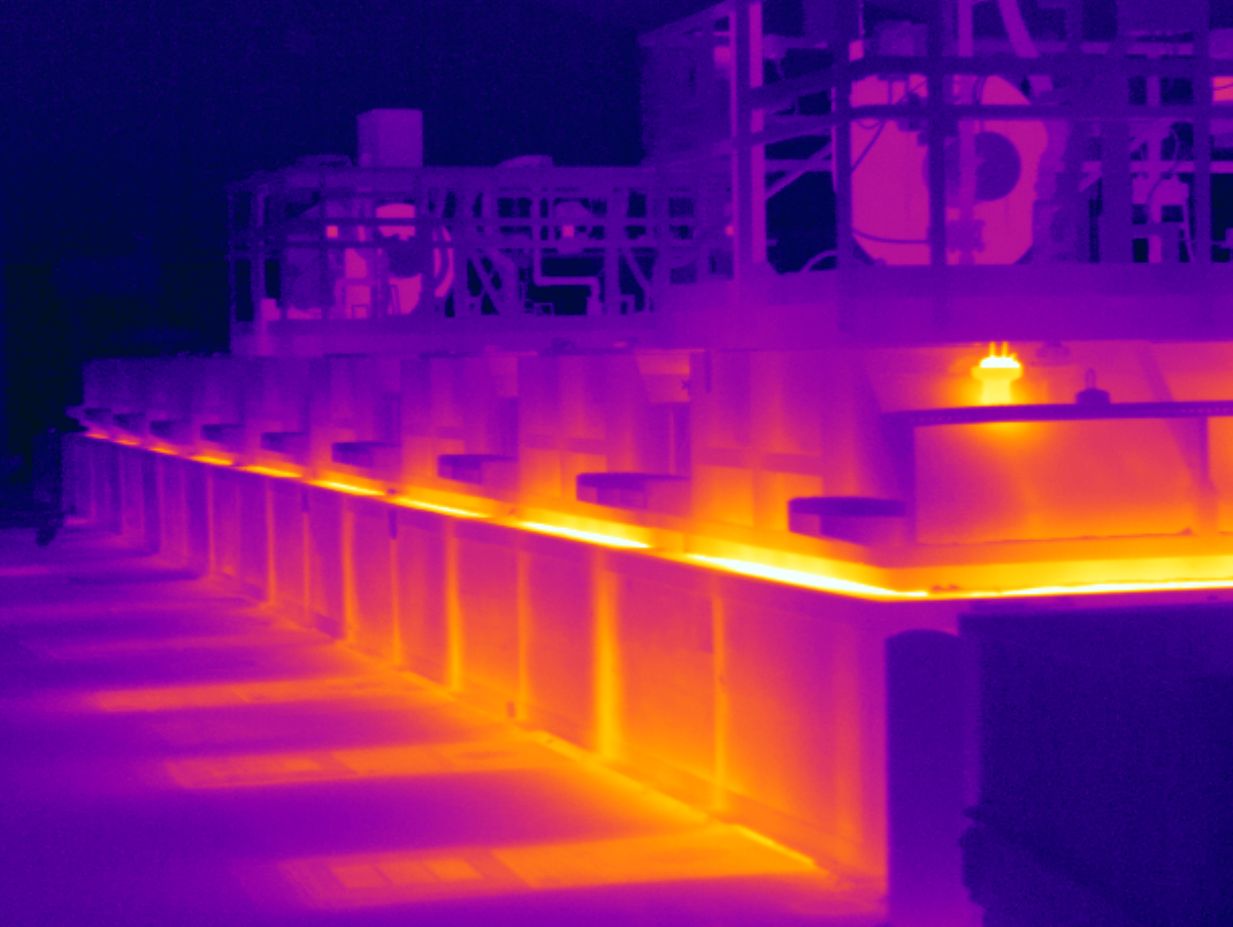

Industrial furnaces still offer a high potential for optimization in terms of cost and energy efficiency as well as the product quality achieved. Optimization approaches relate to furnace insulation, setting plans, kiln furniture used as well as temperature cycles and furnace atmosphere - the latter regarding gas composition and flow. The optimization can be made more efficient if the furnace is not used as a black box in an input-output analysis, but has detailed heat treatment data..
Therefore, a mobile furnace measuring rig was developed at the Fraunhofer-Center HTL, which can be used on site at the industrial furnace without having to interrupt the furnace operation. The following measurements can be carried out with the mobile furnace measuring rig:
- Qualitative 3D thermography
- Quantitative measurement of heat flows at the outer shell
- Interruption-free flow measurement of cooling water
- Interruption-free power measurement of electrical loads
- Measurement of the temperature distribution in the effective volume
- Measurement of the composition of the furnace atmosphere
- Measurement of gas flow in the furnace
- Analysis of furnace exhaust gases
3D thermography and the measurement of heat flows are used to identify heat leakage and to evaluate the resulting losses. The measurements of the cooling water and the electrical loads are used for the preparation of energy balances. The measurements of the furnace atmosphere and temperature distribution, on the other hand, are usually required to assess the quality of the heat process.
The composition of the furnace atmosphere can have a great impact on the results of the heat treatment. Thus, the smallest impurities in the atmosphere of inert gas furnaces can already lead to rejects. The HTL has electrochemical and optical sensors with which critical gas types (e.g., CO, O2, CO2, SO2, NO2, CxHy) can be analyzed in the furnace exhaust gas or - at temperatures of up to 1200 ° C - using a gas sampling lance. Gas Flows can be measured directly in the furnace atmosphere or in the exhaust gas using a differential pressure lance (up to 1200 °C) developed at the HTL or with an impeller anemometer (up to 600 °C).
Knowledge of the temperature distribution in industrial furnaces is of great importance. A homogeneous temperature distribution is decisive for optimum product quality. The HTL center provides measurements of the temperature distribution in various accuracies. These are based on commercially available or special high temperature measuring rings developed at the HTL. The temperature measuring rings are conditioned and calibrated at the HTL before use. In doing so, the scattering of the measurement results can be reduced, and the interpretation of the shrinkage data can be quantitatively converted into temperature differences. The temperature measuring rings are positioned at different points in the furnace chamber and evaluated after the heat process. For the calibration of the temperature measuring rings, the ThermoOptical measurement systems(TOM) are used at the HTL.
Using the mobile furnace test ring, the HTL center carries out potential analyzes on industrial furnaces, which already demonstrate optimization possibilities. Depending on the detail level of the potential analysis, a simplified Finite Element (FR) model of the furnace system can be created from the values measured at the furnace (heat flow, exhaust gas temperatures, atmospheric flows, cooling water temperatures, etc.). Using this model, changes to insulation, gas flows or heating parameters can be visualized, and their effects on the furnace operation and the product can be examined. The heat management in the effective volume of the furnace can also be optimized by FE simulation. By combining the furnace simulation with the simulation of the process kinetics developed at the HTL for drying, debinding, sintering, melt infiltration, an overall optimization can be achieved with regard to product quality and energy efficiency for many heat treatment processes.
The potential analysis and the subsequent FE simulations show different possibilities for optimization. Changes to the process parameters can be implemented frequently without significant investment. Repairs to furnace insulation do not require large investments either. Changes in the kiln furniture or furnace insulation, however, are usually associated with major investments or downtimes. In addition to furnace analysis, the HTL also conducts estimates of the life span of refractory materials and kiln furniture. The customer has the opportunity to assess the impact of the improvements and to carry out a cost-benefit analysis.