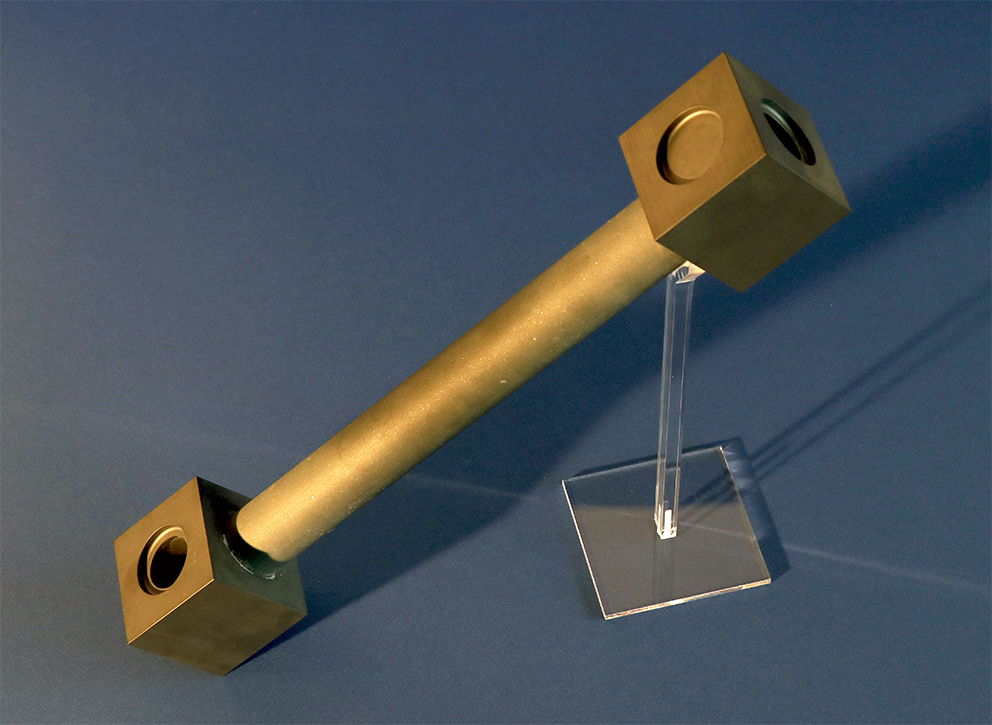
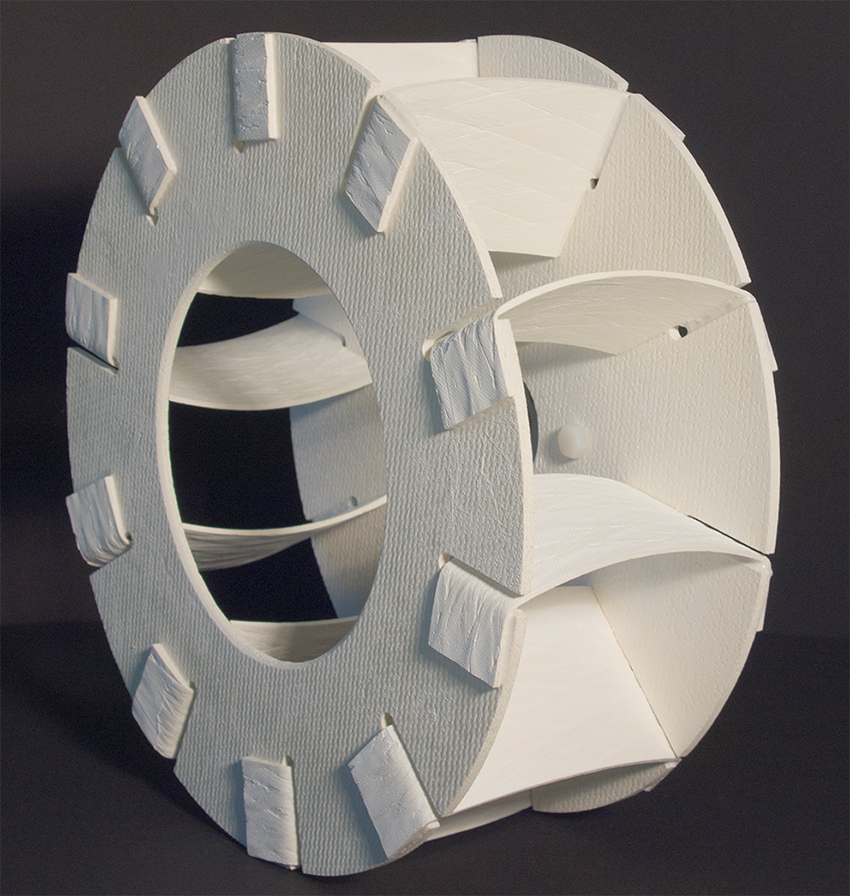
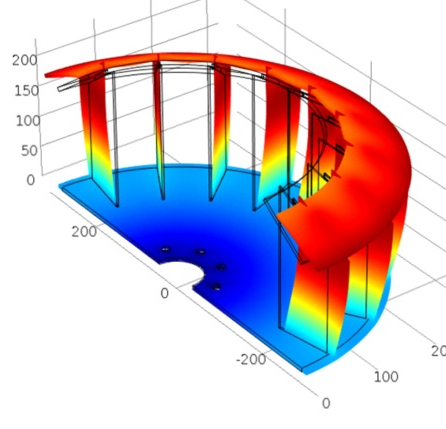
The main focus of industrial heat processes designing is the transfer of heat to the material to be heated and the subsequent cooling. Usually, the heat is transferred by free convection and thermal radiation in the furnace atmosphere, or by heat conduction in the kiln furniture and material to be heated. If the quantity of heat transferred in industrial furnaces is insufficient, special equipment like heat exchangers will be required to improve the heat exchange between fluid media. Recuperators, for example, cause a preheating of the fuel gas in gas-fired furnaces, by utilizing the heat of the furnace exhaust gases in the counter flow principle. In a broader sense, the heat exchangers also include equipment that increase the material flow of the fluids and thus provide an increase in the level of heat exchange, e.g., hot gas ventilators. Heat exchangers for high temperatures and/or corrosive media must be manufactured from ceramics. For oxygen-free atmospheres, heat exchangers can also be made of carbon materials or refractory metals. The heat exchangers must withstand high thermomechanical stresses. There is a need for further development of heat exchangers subjected to high temperatures and corrosive atmospheres.
Heat exchangers used at high temperatures above 1000°C transfer heat between gaseous media. They are frequently designed as tube bundle heat exchangers and operate according to the counter- or cross-flow principle. In order to increase the contribution of radiation to heat transfer, the tube surfaces are frequently textured. One special type is heat exchangers, where the heat is stored temporarily in a solid material which is alternately subjected to the flow of cold and hot gas. These regenerators are used in gas furnaces and guarantee a very efficient exchange of energy between the gas flows. The rapid temperature change load is very high for the regenerator components, which get in contact with the hot and cold gas flows.
Concepts for high temperature heat exchangers are developed at the Fraunhofer-Center HTL. A tube bundle heat exchanger, for example, for rapid heating of special gases in gas-fired furnaces has been designed. The heat exchanger is constructed modularly using standard silicon carbide components. These components have been joined gas-tight with crystallizing glasses at the HTL. The design can be expanded if necessary. Block heat exchangers can be manufactured at the HTL with 3D printing of SiC powders and subsequent melt-infiltration of Si. 3D print is particularly interesting for the manufacture of prototypes or a small batch series. If necessary, the heat exchangers can also be manufactured from other ceramic materials, e.g., aluminum oxide. In addition to monolithic ceramics, the HTL center is also able to produce heat exchangers from fiber-reinforced ceramics (CMC). This is of interest for heat exchanger components that are subjected to particularly high thermomechanical stresses. Depending on the application temperature and atmosphere, oxide and non-oxide CMCs can be used at the HTL. Whereas non-oxide CMCs consist of SiC fiber-reinforced SiC ceramics and are intrinsically gastight, oxide CMCs have to be made gastight by special coatings.
Hot gas ventilators forced gas convection in industrial furnaces. This can be utilized for homogenization of temperature and concentration gradients in the furnace atmosphere, but also to exchange enhanced heat and material flow between different zones in the furnace. For high temperature use, hot gas ventilators are usually constructed as radial fans. These fans cannot consist of metallic components at temperatures exceeding 1000°C, because creep deformation of the materials is too excessive. Due to the high rotation frequency of approx. 100 Hz and rotary speeds of several 100 m/s, there are very high centrifugal forces necessitating new material concepts. Of particular interest, here, are again CMC materials, featuring high elongation at break thanks to the fiber reinforcement. An additional challenge is the balancing of the ventilator wheels, which is significantly more complex for ceramic materials and CMC than for metallic ventilators.
At the HTL, hot gas ventilators can be designed using finite element (FE) analyses. On one hand, the thermomechanical stresses to which the component is subjected at a certain speed of rotation, are calculated. The result can be used to specify the required material properties. On the other hand, the expected benefits of the use of a hot gas ventilator can be determined: e.g. maximum heating and cooling rates can be derived by simulations using a suitable furnace model. For the construction of hot gas ventilators made of CMC components, the HTL has a range of competences available to cover the entire manufacturing chain. Due to the complex geometry of a radial fan, it is generally not manufactured as a single component but consists of several assembled components. The HTL center also has specific competences in the required joining technologies. Radial fans, for example, are manufactured from oxide CMC with fabric made of mullite fibers and a matrix made of aluminum oxide from standard components, which are then joined to build the complete hot gas ventilators using our self-developed crystallizing glass solders.
To validate the functionality and reliability of the hot gas ventilators or heat exchangers, a range of testing and measurement procedures are available at the HTL. With these, all relevant material parameters, particularly elastic and thermophysical properties, as well as flexural strength and crack resistance up to the temperature of application can be determined. In a special, newly developed system (TOM_chem), the degradation effects caused by corrosion or abrasion can be examined under almost real-life conditions on small samples of the material. Furthermore, using non-destructive test procedures (computer tomography, thermography, ultrasonic testing and terahertz wave analysis), complete components can be analyzed for defects or changes to the structure under load.