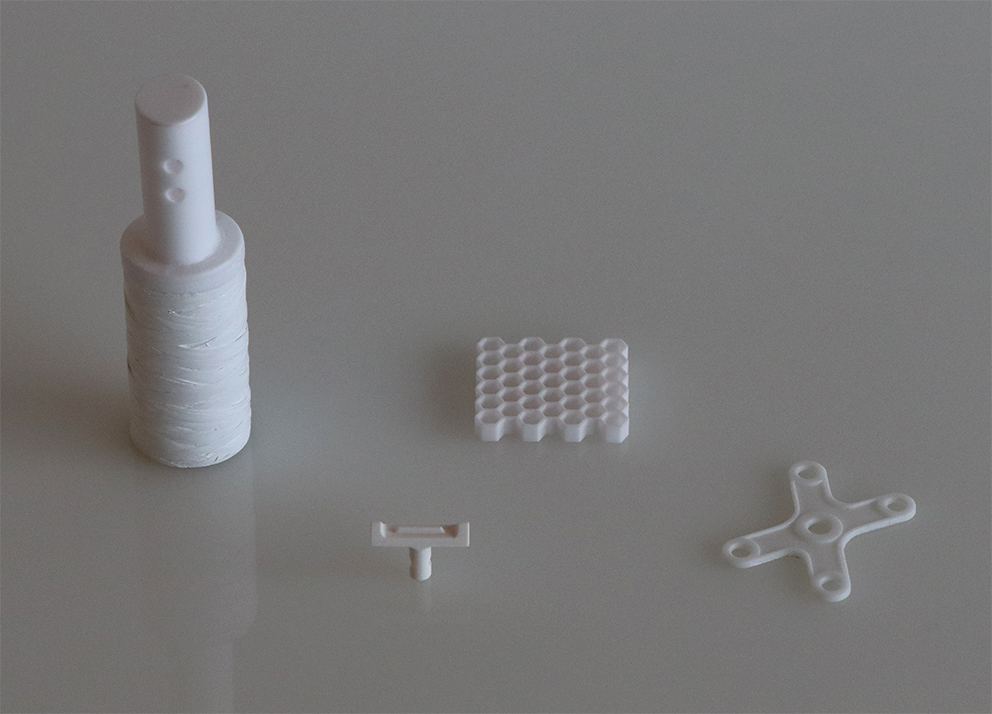
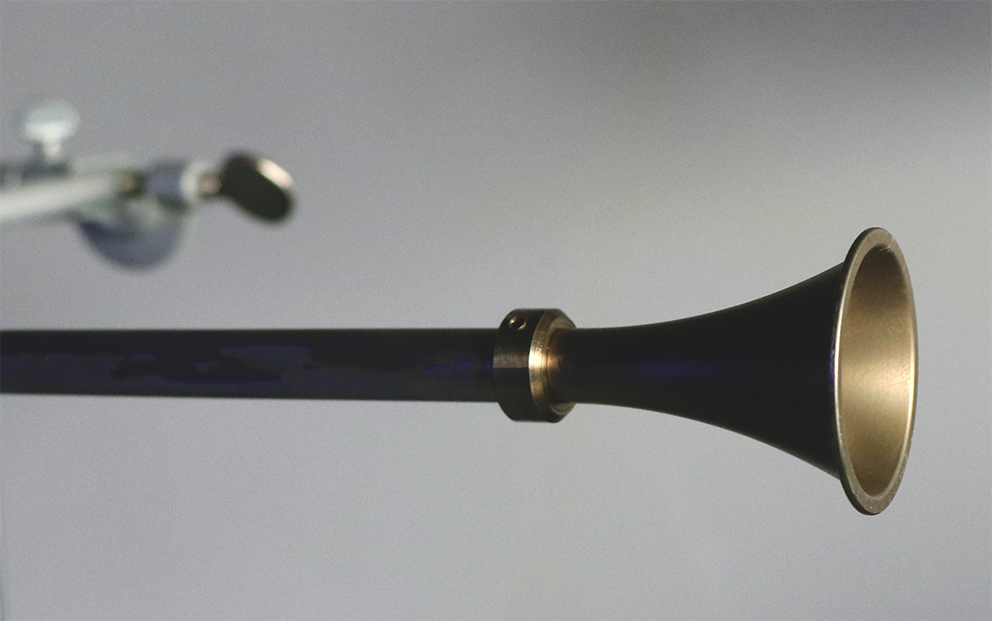
Industrial furnaces are often operated like a black box, as modifications in the thermal process or the furnace equipment - carried out with the intervention to determine process data - can have a negative effect on the temperature distribution in the furnace or other quality-relevant characteristics. Furthermore, high temperatures and aggressive atmosphere in the furnaces are critical for most sensors. Robust high-temperature sensors that can be used in a minimally invasive way are required. For efficient process control, short sensor response times are required, too. The following fields of application are covered by high-temperature sensors:
- Temperature measurement and measurement of heat flows/temperature distributions
- Furnace atmosphere (gas composition/flow)
- Dimension measurements, optical monitoring
- Sound emission, acoustical monitoring
- Viscosity and composition of melts
The Fraunhofer-Center HTL develops high-temperature sensors for different applications in the field of industrial heat treatments. The sensors are usually made of ceramic components in order to withstand the high application temperatures to which they are exposed to. A particularly short response time is achieved by intricate structures manufactured using 3D printing. A particularly high thermal shock resistance is guaranteed by the protective sealing made of CMC (ceramic matrix composites). Corrosion-resistant coatings for high-temperature sensors are manufactured at the HTL from specifically designed crystallizing glasses. Whenever possible, commercially available sensors are integrated. The high-temperature sensors are designed at the HTL center according to customer requirements. Prototypes and small numbers of sensors can be manufactured at HTL. Even the measurement electronics and data evaluation software are developed in house, when necessary. The HTL has test stations available, in which the application performance of the high-temperature sensors can be tested under defined conditions.
At the HTL, temperature senors are usually based on metallic materials that utilize the Seebeck effect or the temperature coefficients of the electrical resistance. The metals can be used as layers which are applied to ceramic substrates or as wires. The encapsulation materials are ceramics or crystallized glasses. The temperature sensors can be designed for sensitive differential temperatures and heat flow measurements. Furthermore, the HTL center has extensive experience in the use of pyrometers for high-temperature measurement of thermal radiation. Pyrometer systems can be designed and calibrated and the measurement software can be adapted to the specific requirements. For example, pyrometers can even be utilized for very fast measurement of temperature changes using specified amplifiers. The large area measurement of temperature fields is performed at the HTL using thermal imagers, whose optics can be adapted to suit the respective application. Temperature distribution in industrial furnaces can also be determined with specially designed temperature measurement rings. The measurement rings are used like dosimeters and indicate the total heat energy absorbed by determining their level of shrinkage due to sintering. They can be conditioned and calibrated at the HTL. Furthermore, temperature measurement rings for special applications, e.g. very high temperatures above 1800°C, are manufactured at the HTL.
For the measurement of furnace atmospheres, the HTL has developed high-temperature sensors which record the flow velocity inside the furnace. They are designed as dynamic pressure sensors in an aluminum-oxide ceramic and feature a protective sleeve made of oxidic CMC (ceramic matrix composites). The composition of the furnace atmosphere is determined preferably with electrochemical sensors. For example, the oxygen activity is determined using the oxygen ion conductivity of zirconium oxide ceramics over a very large range of approx. five orders of magnitude. CO, CO2, SO2, NO2 and CxHy are also recorded using commercially available sensors. The gas composition is measured primarily in the exhaust gas of industrial furnaces. If required, sensors can be manufactured for use in the hot zones of industrial furnaces. Furthermore, the HTL develops gas sampling lances made of CMC with a particularly high thermal shock resistance. The sampled gases can be analyzed subsequently in the laboratory using different analysis methods.
For the contact-free, optical investigation of heat treatment processes, special ThermoOptical measurement methods and systems (TOM) have been developed at the HTL. They include the required openings in the furnace linings, the optical components and the data evaluation algorithms. The TOM principle has been developed so that typical disturbing variables in industrial furnaces, e.g. heat shimmer or condensation of vapors have minimal interference. Simultaneously, the TOM set-up has been developed in such a way that the heat treatment processes are only changed minimally. For this purpose, small openings, light guides and/or auxiliary heaters are used. The data evaluation is performed using robust contour detection and correction algorithms which facilitates the quantitative determination of numerous measured dimensional values.
For acoustical monitoring of thermal processes, special noise emission analysis have been developed at the HTL. The coupling of the microphone to the hot zone of the furnace is via a special stethoscope. Interfering noise is eliminated by the measurement of the differences in the delay times of noise signals from several microphones, installed in the furnace at different locations. Complex parallel algorithms have been developed for the evaluation of the noise signals in real time.
Special sensors are developed according to customer requirements, e.g. for application in melts or particularly corrosive furnace atmospheres.