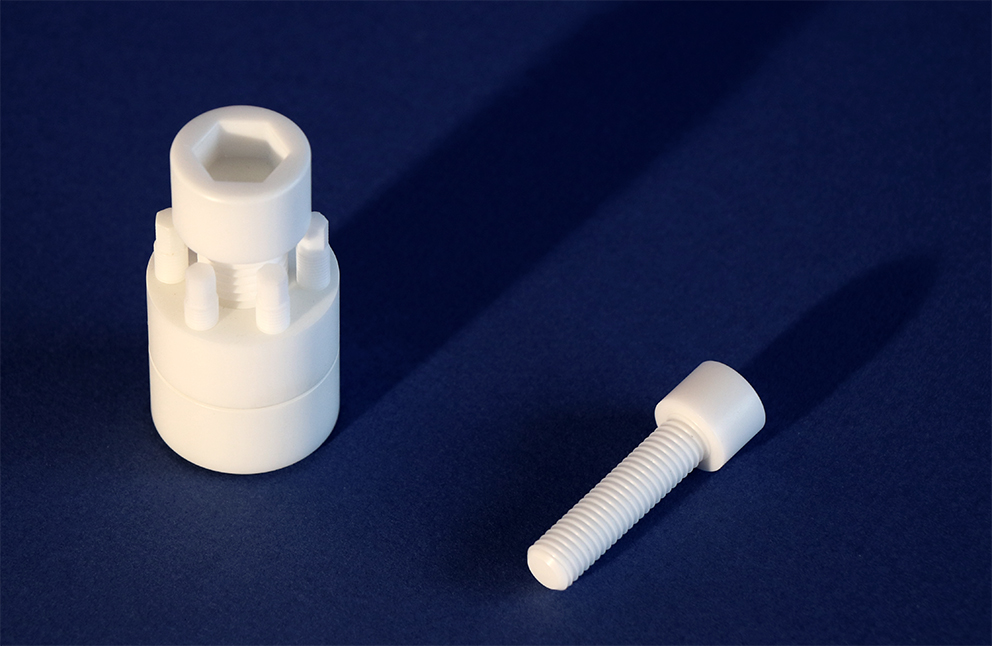
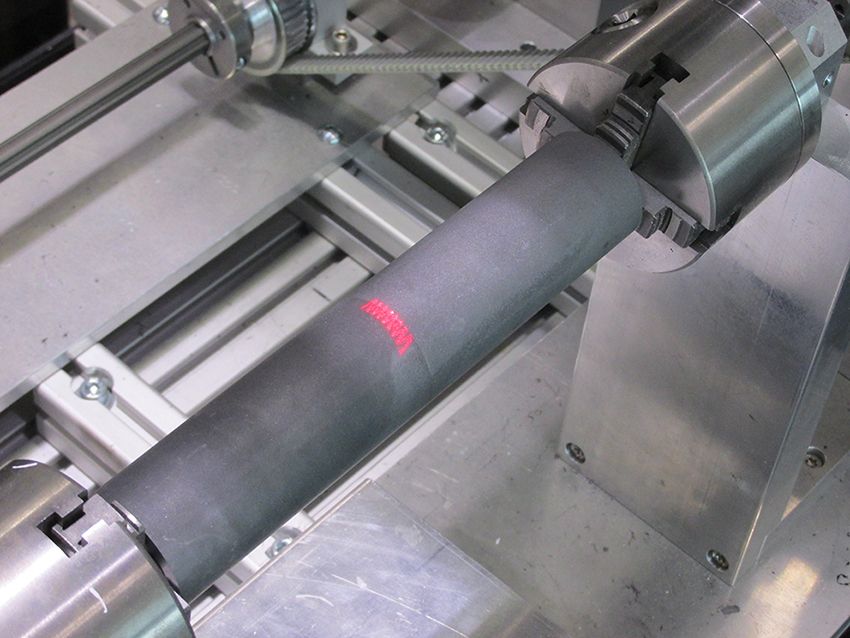
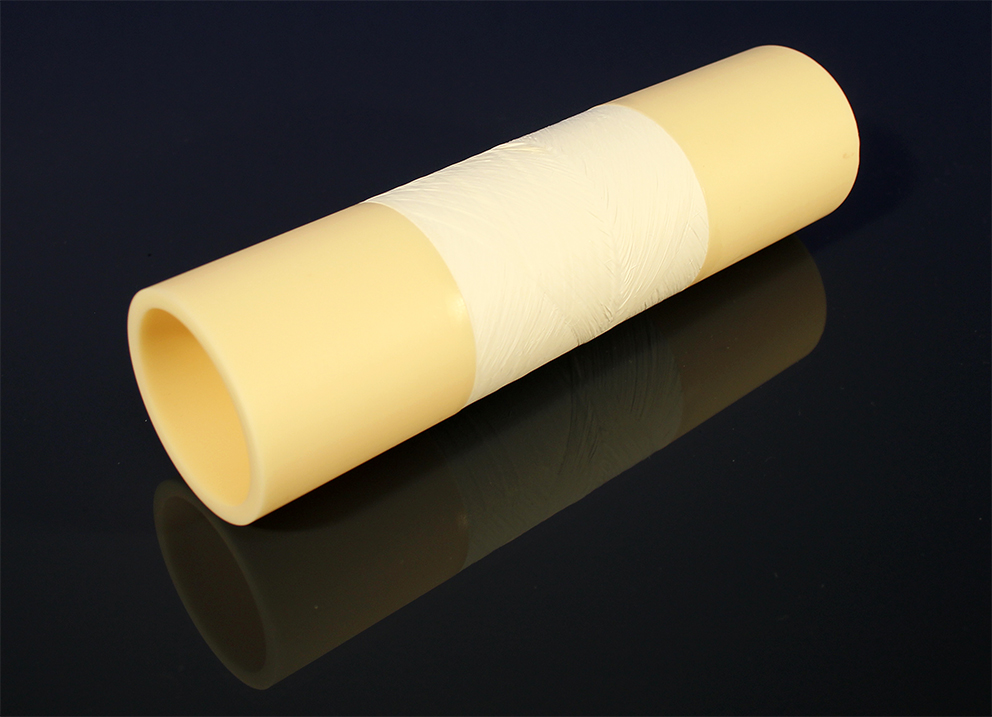
Joining processes enable the manufacture of components with complex geometries from simpler standard components. It, thus, reduces the complexity and the costs of the manufacturing processes. Furthermore, joining partners made of differing materials also play a significant role. As the individual components are manufactured using differing techniques, joining processes are necessary to form composite components. For high-temperature use of joint components, it is self-evident that the joint must also withstand high temperatures. In addition to tensile and flexural strength, a high creep resistance and – in many cases – a high gas tightness of the joint is necessary. Sometimes, it is necessary to implement reversible joints. The joint partners for high-temperature applications are always ceramics or metals.
The Fraunhofer-Center HTL develops soldering and jointing processes for high-temperature applications[1]. The joints include substance-to-substance, positive-fitting and/or friction-locked joints. They can be customer-specifically developed at the HTL for joint partners made of monolithic ceramics, fiber-reinforced ceramics (CMC) or metals. The HTL has the entire process chain for the manufacture of geometrically complex ceramic components and metal-ceramic connected materials at its disposal:
- Construction suitable for joining
- Material processing
- Development of joining materials
- Joining technique
- Characterization and testing of joined connections
For successful joining, a joining-suitable design for joining components and connection points is vital. This is undertaken at the HTL center employing finite element (FE) methods. By simulation of the application behavior of the respective components, the loads in the joint area are determined. The geometry of the connection is optimized, so that there are a minimum of mechanical and thermal stresses. The stresses in the joined connection and the microstructure can be calculated and optimized at varying scale sizes by FE simulation. The joined surface and thus the mechanical load-bearing capacity can be increased by component overlaps or interlocking.
Joining surfaces are frequently created by intermediate machining of the joint partner. Through the machining, the surface qualities can be adapted very easily, and the joining gap can be set precisely. In many cases, the required structures are already created during molding. For example, preforms for fiber-reinforced components with joining-suited fiber structures can be manufactured. The reversible combination made of positive-fitting and friction-locked joints is implemented at the HTL using ceramic screws. The ceramic materials and the thread geometry are optimized for high-temperature application. The threads can be cut cost-effectively in the green or white body state.
The material-fit joints must adapt the solder used exactly to the material to be joined. This particularly concerns the wetting behavior and the thermal expansion coefficients. At the HTL, special crystallizing glass solders are used for the joining process. The glass used features good wetting and low viscosity and can therefore fill the joint gap accurately. The heat treatment causes the glass to crystallize to a large extent. The high crystalline share guarantees the high-temperature strength and creep resistance. The thermal expansion coefficients of these crystallizing glass solders can be set exactly by a glass composition with a wide range between 3.5 *10-6 K-1 and 8.5 *10-6 K-1. For non-oxide ceramics and metals, the used solder is on a Si or metallic basis. The development of the solder is supported by the high-temperature test method available at HTL. With the high-temperature test method, the expansion and wetting behavior of the solder is exactly determined. With the different solders, both similar joinings as well as material joinings, such as ceramic-CMC, ceramic-metals or CMC-metals, can be implemented. Frequently used ceramic materials for the joining process are monolithic ceramics such as mullite, Al2O3, SSiC or AlN and CMC materials like oxidic (O-CMC) or non-oxide fiber-ceramics (C-SiC, SiC-SiC)[2].
For the join process with solders, they must be “melted”. With heat treatment, no distortion may occur in the joining components, and the thermal stresses may not enter the inherent strength range. Join processes are realized at the HTL using differing systems. If low-stress heat treatment or a controlled atmosphere are at the forefront, conventional join processes are undertaken using furnace heating. At the HTL, very different kinds of furnaces for inert gas, reducing gas atmospheres, vacuums or oxidic atmospheres with varying usable volumes are available. The process times amount to several hours up to a day, depending on the heat-up and cooling speed and hold times. Due to batch processes in large furnace systems up to 0.4m³ usable volume, large part counts can also be processed. The processes prove to be very stable due to the well definable parameters. Alternatively, joinings at the HTL can also be undertaken by laser heating. With the assistance of laser technology, individual components can be joined in a matter of minutes to form a complex completed component. In the process, only the join area is selectively heated, resulting in benefits if the distortion of components due to warming in the furnace is to be worried about or if the join surface is very small in comparison to the component size. The laser employed is either a CO2 laser or a diode laser. The laser beam is moved quickly relative to the join area to achieve the desired low stress temperature distribution. To determine the parameters, preliminary temperature simulations are undertaken. Process monitoring is assured via pyrometry and IR cameras[3]. Use of variable clamping devices ensures that components of varying geometry can be clamped, at the join area locally heated and joined with a great degree of shaping precision. The gas atmosphere can be changed during laser joining by an inert gas flow.
The quality of the produced joined connections is evaluated at the HTL using different testing methods. Standard-compliant mechanical test procedures are employed for shear strength and flexural strengths at room temperature and high-temperature up to 1500 °C. The creep properties are determined in a similar way. For evaluation of the composite components or large surface joinings, the non-destructive test procedures available at the HTL, such as computer thermography (CT), terahertz wave analysis or thermography are ideal. These methods enable a visual representation of the solder distribution, provide an insight on any existing material defects, such as pores or cracks, and thus ensure a quality test of joined samples and components. For determination of the seal tightness of joined connections, at the HTL the gas tightness is tested compliant to the DIN EN 1779 standard at temperatures up to 1000 °C. To examine the microstructure in the joined area, phase analyses using diffractometers and joined area analyses with scanning electron microscopes and light microscopes are undertaken.
[1] Gadelmeier, C.; Schmidt, J.: Joining of Ceramic and Metal Parts. CERAMIC APPLICATIONS 1 (2017), p. 59
[2] Gadelmeier, C.; Schmidt, J.; Göthe, M.; Jovanovic, D.: Characterization of Furnace sintered mullite and oxide ceramic matrix composites (O-CMC) by using glass solders. Advances in science and technology Vol. 88 (2014), pp. 162-171
[3] Gadelmeier, C.; Schmidt, J.; Jovanovic, D.; Zietkowski, M.; Eckardt, C.: Adhesive bonding of ceramics for complex ceramic parts in high temperatures furnaces. Material Science Forum Vol. 825-826, 2015, pp. 279-286