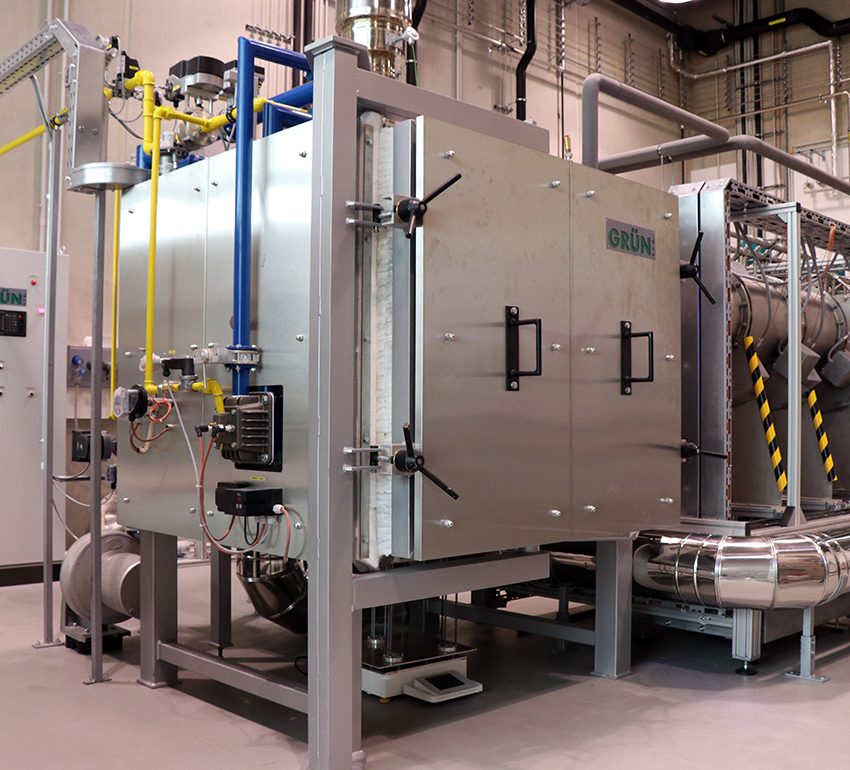
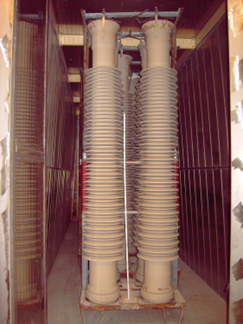
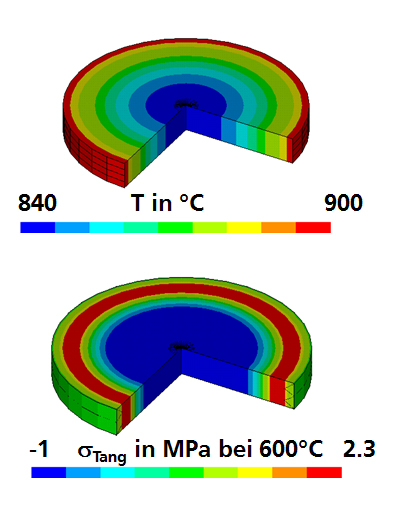
Bei der Herstellung von Silikatkeramiken trägt die Wärmebehandlung wesentlich zur Produktqualität und den Herstellkosten bei. Es lohnt sich deshalb, die Prozessparameter bei der Wärmebehandlung zu optimieren. Bei der Trocknung, dem Binderausbrand, der Quarzumwandlung und der Entwässerung müssen Verfahren identifiziert werden, die einerseits einen möglichst hohen Durchsatz ermöglichen, aber andererseits die Schadensfreiheit der Bauteile gewährleisten. Beim Brennen wird eine endformnahe Herstellung mit engen Fertigungstoleranzen und guten Materialeigenschaften angestrebt. Beispielsweise können mit geeigneten Brennbedingungen neue Designs realisiert werden. Aus Kostengründen sollen der Durchsatz durch den Brennofen maximiert und dessen Energieverbrauch und Wartungsaufwand minimiert werden. Die Ausschussrate ist zu minimieren.
Die am Fraunhofer-Zentrum HTL eingesetzten Methoden eignen sich für alle Arten von Silikatkeramiken: Porzellan, Steingut oder Steinzeug und auch silikatische Feuerfestwerkstoffe. Kleine Bauteile können ebenso optimiert werden, wie mehrere Meter lange Hochspannungsisolatoren aus Porzellan oder Rohre aus Steinzeug. Für die Erfassung der notwendigen In-Situ-Messdaten stehen am Fraunhofer-Zentrum HTL geeignete ThermoOptische Messanlagen (TOM) zur Verfügung. Diese können an Luft, aber auch mit der Atmosphäre gasbeheizter Öfen betrieben werden. Alle für die Optimierung der Wärmebehandlung von Silikatkeramiken erforderlichen Materialeigenschaften können in situ gemessen werden. Die In-Situ-Messungen erfolgen an Proben mit einem Volumen bis zu 30 cm³. Die Hochskalierung auf den Bauteilmaßstab wird mit Finite-Elemente (FE)-Verfahren durchgeführt. Für alle wesentlichen Wärmebehandlungsschritte an Silikatkeramiken stehen entsprechende FE-Modelle zur Verfügung. Mittels FE-Simulation werden die Prozessparameter optimiert und experimentell verifiziert. Im letzten Schritt werden die optimierten Prozessparameter dann auf den Produktionsofen übertragen.
Bei der Trocknung muss das in den Scherben noch enthaltene Wasser entfernt werden, ohne dass es zu Schäden kommt. Aufgrund der kleinen Poren können erhebliche Trocknungsspannungen auftreten. Zu schnelle oder ungleichmäßige Trocknung führt zu Rissen oder Verzug. Dabei sind die lokalen Trocknungsraten stark von der relativen Feuchte, der Temperatur und der Luftströmung abhängig. Das Fraunhofer-Zentrum HTL verfügt über eine Vorrichtung, mit der Scherben unter kontrollierter Feuchte, Temperatur und Gasströmung während der Trocknung gewogen werden können. Auf diese Weise kann die Trocknungsrate während der verschiedenen Trocknungsstadien ermittelt werden. In den kritischen Stadien kann die Trocknungsrate gezielt abgesenkt werden. Der Verzug der Scherben durch ungleichmäßige Trocknung wird in FE-Modellen simuliert, bei denen die Luftströmung und der lokale Feuchtegradient berücksichtigt werden. Bei der Optimierung werden Feuchte- und Strömungsmessungen in den industriellen Trocknungsaggregaten berücksichtigt.
Enthält die Masse organische Additive, so entsteht bei deren Ausbrand Verbrennungswärme. Im Inneren der Grünteile, wo die Sauerstoffkonzentration während des Binderausbrands sehr gering ist, können gleichzeitig Pyrolysereaktionen ablaufen, die Wärme verbrauchen. Die entstehenden Temperaturunterschiede bewirken thermische Spannungen, die wiederum zu Rissen oder zur Zerstörung der Grünteile führen können. Bei zu schnellem Binderausbrand können die entstehenden Gase nicht rasch genug aus den Porenkanälen an die Bauteiloberfläche transportiert werden. Der entstehende Überdruck in den Porenkanälen führt ebenfalls zu Bauteilschäden. Ähnlich wie bei der Trocknung gilt es, das schnellste noch sichere Temperaturprofil zu finden, mit dem der Binderausbrand noch fehlerfrei durchgeführt werden kann. Strömungsgeschwindigkeit und Zusammensetzung der Ofengase können dabei in vielen Fällen variiert werden. Analog zur Trocknung werden Experimente zum Binderausbrand in kontrollierter Atmosphäre und Temperatur durchgeführt. Der Reaktionsgrad wird durch kontinuierliche Messung der Probenmasse, Rissbildungen durch Schallemissionsanalyse detektiert. Die Optimierung der Prozessparameter erfolgt analog zur Trocknung mittels FE-Simulation, die Verifizierung der optimierten Bedingungen durch zusätzliche Experimente an großen Bauteilen. Für den Test zum Binderausbrand an großen Bauteilen steht am Fraunhofer-Zentrum HTL ein gasbeheizter Messofen, TOM_gas, zur Verfügung. An diesem Ofen können Grünteile mit einer Masse bis 15 kg während des Binderausbrands gewogen werden.
Die Entwässerung findet bei Silikatkeramiken statt, wenn die Scherben zu höheren Temperaturen aufgeheizt werden – etwa zwischen 500°C und 700°C. Dabei wird das in den Tonrohstoffen enthaltene Kristallwasser aus den Scherben entfernt (Dehydratation). Beispielsweise wandelt sich Kaolinit durch Dehydratation in Metakaolin um. Bei zu rascher Aufheizung kann der im Inneren der Scherbenr freigesetzte Wasserdampf nicht rasch genug entweichen. Es kommt zum Druckanstieg, der zur Zerstörung der Scherben führen kann. Im gleichen Temperaturbereich bei ca. 573°C findet auch noch die Umwandlung der in den Scherben enthaltenen Quarz-Rohstoffe statt. Dabei wandelt sich der Quarz in seine Hochtemperaturmodifikation um und dehnt sich um ca. 0,8% aus (Quarzsprung). Die Volumenzunahme erzeugt mechanische Spannungen, die ebenfalls zu Schäden am Bauteil führen können. Die Optimierung der Prozessparameter während der Entwässerung erfolgt durch In-Situ-Messungen der Gewichtsänderungen und ggf. der Dehnungen und nachfolgende FE-Simulation. Die Verifizierung der optimierten Prozessparameter kann dann an großen Bauteilen mittels TOM_gas durchgeführt werden. Ähnliche Optimierungsstrategien wie bei der Entwässerung werden auch eingesetzt, wenn in den Rohstoffen Carbonate enthalten sind. Diese zersetzen sich im Temperaturbereich um 800°C bis 900°C, wobei die freiwerdenden Gase ebenfalls zu einem Überdruck im Inneren der Scherben führen können.
Beim Brennen von Silikatkeramiken soll eine Verdichtung mit definierter Restporosität erreicht werden. Das Gefüge soll fehlerfrei und homogen sein, und das Bauteil darf sich nicht verziehen. Falls Glasuren eingesetzt werden, müssen diese frei von Fehlern wie Nadelstichen oder Blasen sein. Abweichungen von der Soll-Geometrie entstehen beim Brennen durch eine ungleichmäßige Verteilung der Porosität im Scherben sowie durch den Einfluss von Reibung, Gravitation und Temperaturunterschiede bei der Wärmebehandlung:
- Die ungleichmäßige Porositätsverteilung im Scherben kann durch die Formgebung verursacht sein – z.B. durch Sedimentationseffekte beim Schlickerguss. Sie wird am Fraunhofer-Zentrum HTL mit sehr empfindlichen Messverfahren detektiert.
- Reibung und Gravitation führen zum Verzug der Scherben, wenn deren Standfestigkeit zu gering ist. Kritisch ist besonders der Bereich oberhalb von 1000°C, bei dem sich viel Schmelzphase ausbilden kann und stabilisierende Reaktionen wie die Bildung von Sekundärmullit noch unzureichend gegenwirken.
- Temperaturunterschiede innerhalb der Bauteile führen beim Brennen zum Verzug. Größere Temperaturunterschiede in den Bauteilen können auch Risse auslösen oder zur Zerstörung der Bauteile führen. Temperaturunterschiede im Ofen führen zu Streuungen in der Restporosität und den Bauteilabmessungen.
Wenn in den Rohstoffen Eisenoxid enthalten ist, ist auch die Umwandlung des dreiwertigen zum zweiwertigen Eisen zu beachten, die an Luft bei ca. 1200°C stattfindet. Der bei dieser Umwandlung freigesetzte Sauerstoff muss die Bauteile durch die Porenkanäle verlassen können. Sind die Poren aufgrund starker Sinterschwindung bereits geschlossen, kommt es zu einem Aufblähen der Scherben. Als Gegenmaßnahme müssen reduzierende Atmosphären verwendet werden, die die Temperatur der Eisenoxidumwandlung herabsetzen. Gasphasenprozesse führen häufig zu Glasurfehlern. Mittels optischer Dilatometrie und Wägung kann das Sinter- und Entgasungsverhalten von Glasuren am Fraunhofer-Zentrum HTL gemessen und optimiert werden.
Die Sinterschwindung der Scherben wird mit den TOM-Anlagen exakt gemessen. Dabei wird die Atmosphäre gasbeheizter Öfen exakt nachgestellt. Zusätzlich werden weitere wichtige Materialeigenschaften zum Wärmetransport und zur Kriechverformung während des Brennens erfasst. Mittels gekoppelter FE-Modelle werden die thermomechanischen Effekte im Bauteil simuliert und die Prozessparameter optimiert. Neben der Ofenatmosphäre und dem Brennzyklus können dabei auch Brennhilfsmittel berücksichtigt werden, die einen großen Einfluss auf die Temperaturverteilung im Scherben haben und ggf. zur Unterstützung von Scherben mit geringer Standfestigkeit eingesetzt werden müssen. Die Optimierung ist für Glüh- und Glattbrandprozesse ebenso möglich wie für den Schnellbrand. Die Verifizierung der optimierten Prozessparameter kann an großen Silikatkeramiken-Bauteilen mittels TOM_gas durchgeführt werden.