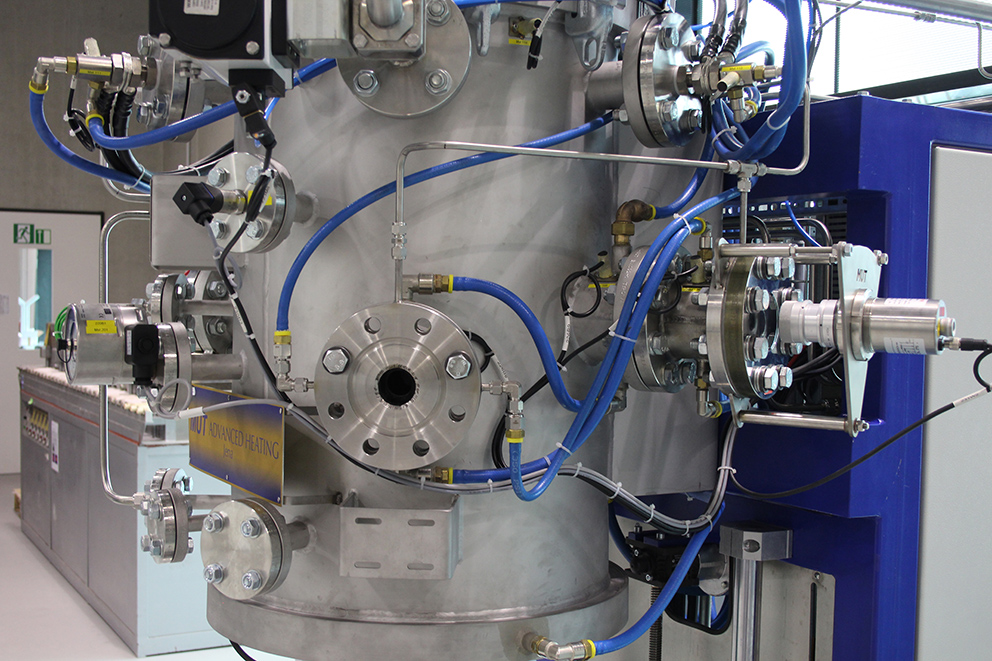
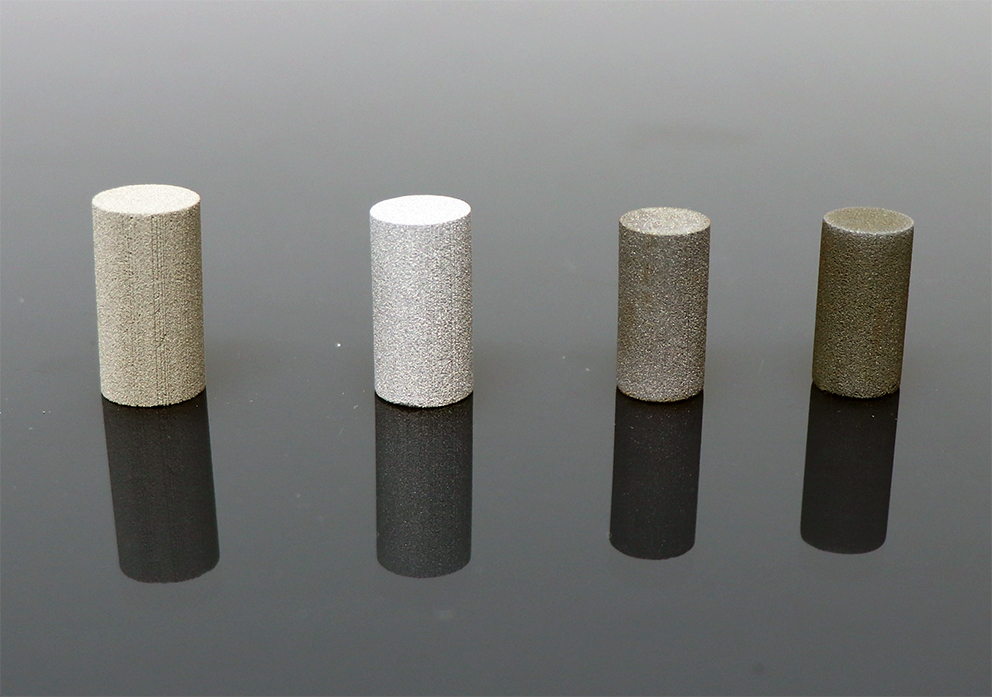
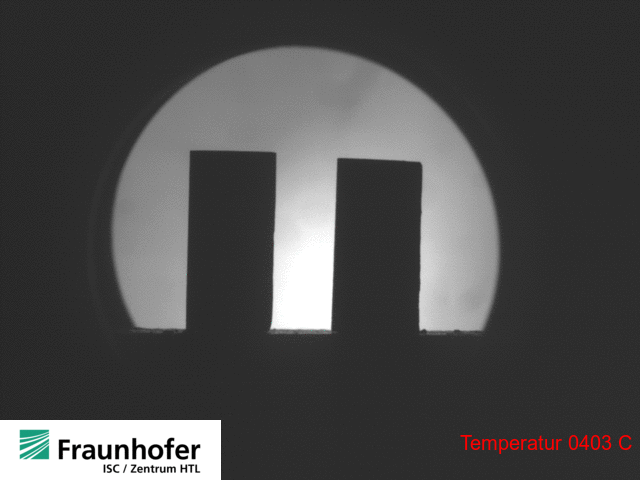
Im Unterschied zur Schmelzmetallurgie werden in der Pulvermetallurgie (PM) Metallbauteile aus pulverförmigen Ausgangsstoffen durch einen Formgebungs- und Sinterprozess hergestellt. Ein großer Vorteil der pulvermetallurgischen Herstellroute ist die Verringerung des Endbearbeitungsaufwands. Dies zahlt sich besonders bei Bauteilen mit komplizierter Geometrie aus, die in großen Stückzahlen, z.B. im Pulverspritzguss-Verfahren, gefertigt werden können (PIM=Powder Injection Molding). Typische in der Pulvermetallurgie verwendete Metalle sind Eisen bzw. Stähle, Aluminium, Kupfer und Bronze. Um den Kostenvorteil gegenüber der schmelzmetallurgischen Herstellung zu realisieren, ist allerdings eine präzise endformnahe Sinterung der PM-Bauteile erforderlich. Nach der Sinterung sollten möglichst weder eine Kalibrierung noch eine Endbearbeitung oder ggf. nur noch die Endbearbeitung von Funktionsflächen erforderlich sein. Ein weiterer Vorteil der Pulvermetallurgie ist, dass über den Herstellprozess - Pulverherstellung und Mischung sowie die anschließende Formgebung und Sinterung - Gefüge sehr gezielt eingestellt werden können. So ermöglicht die Pulvermetallurgie die Herstellung von Bauteilen aus Kompositen oder Legierungen, die schmelzmetallurgisch nicht erzeugt werden können, z.B. Hartmetalle, Diamantverbundwerkstoffe, Magnetwerkstoffe, Nickelbasislegierungen oder Refraktärmetalle. Um die angestrebten Gefüge tatsächlich zu erreichen, ist eine sorgfältige Optimierung der Wärmebehandlung erforderlich. Mikrorisse und Blasen sind zu vermeiden, auf den Metallpartikeln vorhandene Oxidschichten müssen durch Reduktionsprozesse entfernt werden, und ein Übersintern bzw. auch ein Verzug der Bauteile muss ausgeschlossen werden. Gleichzeitig sollen die Herstellkosten minimiert werden. Das heißt, der Durchsatz durch den Sinterofen soll maximiert und dessen Energie- und Wartungskosten abgesenkt werden.
Die Optimierung der Wärmebehandlung kann am Fraunhofer-Zentrum HTL für alle Arten von pulvermetallurgischen Werkstoffen durchgeführt werden. Für die Erfassung der notwendigen In-situ-Messdaten stehen ThermoOptische Messanlagen (TOM) mit sehr unterschiedlichen Atmosphären zur Verfügung. Sinterungen können in Graphit- oder Wolfram-beheizten TOM-Öfen durchgeführt werden. Als Ofenatmosphären können Inertgase oder synthetisch gemischte reduzierende Gase – auch 100% Wasserstoff – eingesetzt werden. Eine TOM-Anlage, TOM_metal, wurde speziell für die In-situ-Messung in der Pulvermetallurgie entwickelt. TOM_metal kann mit Vakuum, Wasserstoff oder anderen reduzierenden Gasen, Inertgas sowie Überdruck (bis 30 bar) betrieben werden. Die In-situ-Messungen erfolgen an Proben oder kleinen Bauteilen mit einem Volumen von ca. 1 cm³ bis 30 cm³. Die Hochskalierung auf größere Bauteile erfolgt mit Finite-Elemente (FE)-Verfahren. Für die Wärmebehandlungsschritte Trocknen, Entbindern und Sintern stehen am HTL entsprechende FE-Modelle zur Verfügung.
Eine Trocknung ist erforderlich, wenn die PM-Grünteile mit plastischen Formgebungsverfahren hergestellt werden. Das in den Grünteilen noch enthaltene Lösungsmittel muss schonend entfernt werden, bevor die Hochtemperaturprozesse gestartet werden können. Zu schnelle oder ungleichmäßige Trocknung führt zu Rissen oder Verzug. Dabei sind die lokalen Trocknungsraten stark von der relativen Feuchte, der Temperatur und der Strömungsgeschwindigkeit des Trocknungsgases abhängig. Das HTL verfügt über eine Vorrichtung, mit der Proben unter kontrollierter Lösungsmittelfeuchte, Temperatur und Gasströmung während der Trocknung gewogen werden können. Auf diese Weise kann die Trocknungsrate während der verschiedenen Trocknungsstadien ermittelt werden. In den kritischen Stadien kann die Trocknungsrate gezielt abgesenkt werden. Der Verzug der Bauteile durch ungleichmäßige Trocknung wird in FE-Modellen simuliert, bei denen die Gasströmung und der lokale Feuchtegradient berücksichtigt werden. Bei der Optimierung können Feuchte- und Strömungsmessungen in den industriellen Trocknungsaggregaten berücksichtigt werden.
Bei der Entbinderung werden die in den PM-Grünproben enthaltenen organischen Formgebungsadditive – in der Regel thermisch - entfernt. Die organischen Additive werden dabei pyrolysiert. Bei zu schneller Entbinderung können die entstehenden Gase nicht rasch genug aus den Porenkanälen an die Bauteiloberfläche transportiert werden. Der entstehende Überdruck in den Porenkanälen kann zu Bauteilschäden führen. Daneben gibt es noch weitere unerwünschte Phänomene, die bei der Entbinderung auftreten können, z.B. die Absorption von Schwelgasen durch kältere Grünteile in kontinuierlichen Öfen oder die Segregation des flüssigen Binders in den Porenkanälen. Außerdem muss dafür gesorgt werden, dass der bei der Pyrolyse u.U. gebildete Kohlenstoff nicht unerwünschte Auswirkungen auf den Sinterverlauf bzw. die Produkteigenschaften hat. Ähnlich wie bei der Trocknung gilt es, das schnellste noch sichere Temperaturprofil zu finden, mit dem die Entbinderung fehlerfrei durchgeführt werden kann. Analog zur Trocknung werden Entbinderungsexperimente am HTL bei kontrollierter Atmosphäre und Temperatur durchgeführt. Der Entbinderungsgrad wird durch Messung der Probenmasse in situ detektiert. Die Optimierung der Entbinderungsparameter erfolgt analog zur Trocknung mittels FE-Simulation, die Verifizierung der optimierten Bedingungen durch zusätzliche Entbinderungsexperimente.