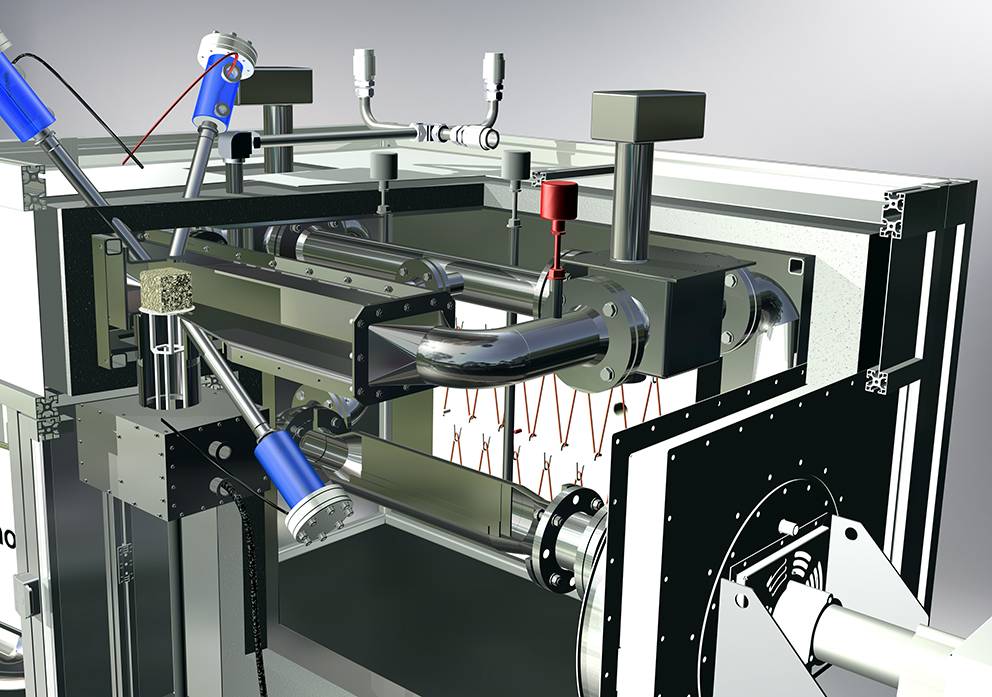
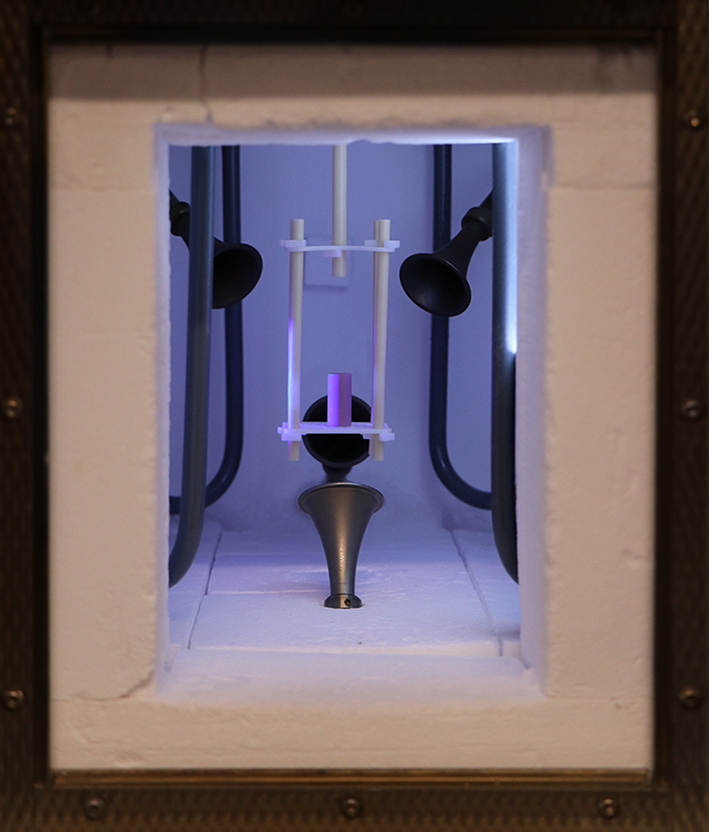

Die Entbinderung von Grünkörpern wird mit den ThermoOptischen Messverfahren (TOM) sowie mit herkömmlichen Thermoanalyseverfahren am Fraunhofer-Zentrum HTL in-situ gemessen und anschließend optimiert. Die Optimierung erfolgt für alle Arten von Grünkörpern, unabhängig von der Bauteilgröße und Geometrie, den anorganischen Komponenten (Metalle oder Keramiken) und der Art des organischen Binders bzw. dem Bindergehalt. So können z.B. auch Entbinderungsprozesse für die üblicherweise schwierig zu entbindernden Grünteile aus Spritzgussverfahren entwickelt werden.
Das Ergebnis der Entbinderung wird von der Ofenatmosphäre beeinflusst. Während bei Entbinderungen an Luft oder anderen sauerstoffhaltigen Ofenatmosphären die Verbrennung der organischen Additive dominiert, sind Pyrolyseprozesse für Entbinderungen in inerten oder reduzierenden Atmosphären relevant. Letztere laufen auch häufig bei Entbinderungen an Luft im Inneren von Grünkörpern ab, weil Sauerstoff dort erst hingelangt, wenn der Binderausbrand in den Randschichten abgeschlossen ist.
Für alle relevanten Ofenatmosphären stehen am Fraunhofer-Zentrum HTL geeignete In-situ-Messanlagen zur Verfügung. Als Ofenatmosphären können Inertgase, oxidische oder reduzierende Gase, auch 100% Wasserstoff, eingesetzt werden. Auch die Ofenatmosphäre in gasbeheizten Öfen kann exakt nachgestellt werden. Der Abgleich der Ofenatmosphären zwischen dem Produktionsofen und der jeweils eingesetzten TOM-Anlage ist wichtig, weil nur so die mittels TOM-Anlage optimierten Entbinderungsbedingungen auf den Produktionsofen übertragen werden können.
Durch die Messung des Probengewichts kann der Entbinderungsgrad mit sehr hoher Reproduzierbarkeit gemessen werden[1]. Die Reproduzierbarkeit beträgt 0,1%. Dies ermöglicht die Erstellung einer aussagekräftigen Datenbasis für die Berechnung der Entbinderungskinetik. Dazu werden am Fraunhofer-Zentrum HTL mehrere Entbinderungen mit unterschiedlichen Temperatur-Zeit-Zyklen an den gleichen Grünproben durchgeführt. Aus den Messdaten wird mit einem robusten numerischen Verfahren ein Kinetik-Modell errechnet, das es erlaubt, den Entbinderungsgrad für beliebige Temperatur-Zeit-Zyklen, die im Rahmen des vermessenen Bereichs liegen, vorherzusagen[2]. Mit diesem Kinetik-Modell sind bereits einfache Optimierungen des Entbinderungszyklus möglich. So können Temperatur-Zeit-Zyklen berechnet werden, bei denen die Entbinderungsrate nahezu konstant ist. Dies führt zu geringeren Belastungen der Bauteile als Temperatur-Zeit-Zyklen, mit konstanten Aufheizraten[3]. Die maximale noch sichere Entbinderungsrate wird dann mit entsprechend berechneten Temperatur-Zeit-Zyklen experimentell ermittelt. Dazu werden die Entbinderungen an größeren Proben bzw. kleinen Bauteilen in den TOM-Anlagen durchgeführt, und während der Entbinderung werden auftretende Probenschädigungen in situ registriert. Zur Registrierung von Schädigungen werden am Fraunhofer-Zentrum HTL in erster Linie Schall- bzw. Gasemissionsmessungen verwendet, weil diese bereits leichte Schädigungen empfindlich registrieren.
Für genauere Untersuchungen, z.B. zum Hochskalieren auf andere Bauteilgeometrien und zur Berücksichtigung von Effekten im Industrieofen sind jedoch weitere In-Situ-Messungen erforderlich. So müssen die endo- bzw. exothermen Effekte bei Pyrolyse bzw. Binderausbrand quantifiziert werden, was am Fraunhofer-Zentrum HTL mittels dynamischer Wärmestromkalorimetrie (DSC) in kontrollierter Atmosphäre durchgeführt wird. Die Temperaturleitfähigkeit der Grünteile wird während der Entbinderung mittels Laser-Flash-Verfahren bestimmt. Zusätzlich wird die Permeabilität von Gasen durch die Porenkanäle des Grünkörpers gemessen. Zusammen mit dem Kinetik-Modell werden diese Messdaten in einem gekoppelten Finite-Elemente (FE)-Modell eingesetzt, das am Fraunhofer-Zentrum HTL zur Optimierung von Entbinderungsprozessen entwickelt wurde. Mit dem Modell wird die Temperaturverteilung im Grünkörper während der Entbinderung für jeden Zeitschritt berechnet, wobei die Reaktionswärme berücksichtigt wird. Aus der lokalen Temperatur und dem lokal verfügbaren Sauerstoff wird mit dem Kinetik-Modell die lokale Entbinderungsrate berechnet. Die daraus resultierenden Gasphasenreaktionen führen zu Konzentrations- und Druckgradienten, die durch Diffusions- bzw. Strömungsvorgänge in den Porenkanälen abgebaut werden. Auch diese Prozesse werden mittels FE simuliert. Zuletzt werden für den jeweiligen Zeitschritt die aus Temperaturunterschieden und dem Gasüberdruck resultierenden mechanischen Spannungen berechnet. Dann wird die Simulation für den nächsten Zeitschritt wiederholt, bis die Entbinderung abgeschlossen ist. Die Entbinderungsbedingungen werden mit dem FE-Modell variiert, sodass die mechanischen Spannungen im Grünkörper minimal werden. Auf diese Weise können die Entbinderungsbedingungen für einzelne Bauteile gezielt optimiert werden. Entbinderungszyklen können im Vergleich zu empirisch optimierten Zyklen drastisch verkürzt werden.